K & S Contracting specializes in foundation repair for homeowners across Saskatchewan. In addition, they also offer general contracting services to Saskatoon and the surrounding area. In their latest Trusted Saskatoon tip, K & S Contracting, Trusted Saskatoon General Contractors, and foundation specialists, discuss concrete foundation cracks, and what they mean.
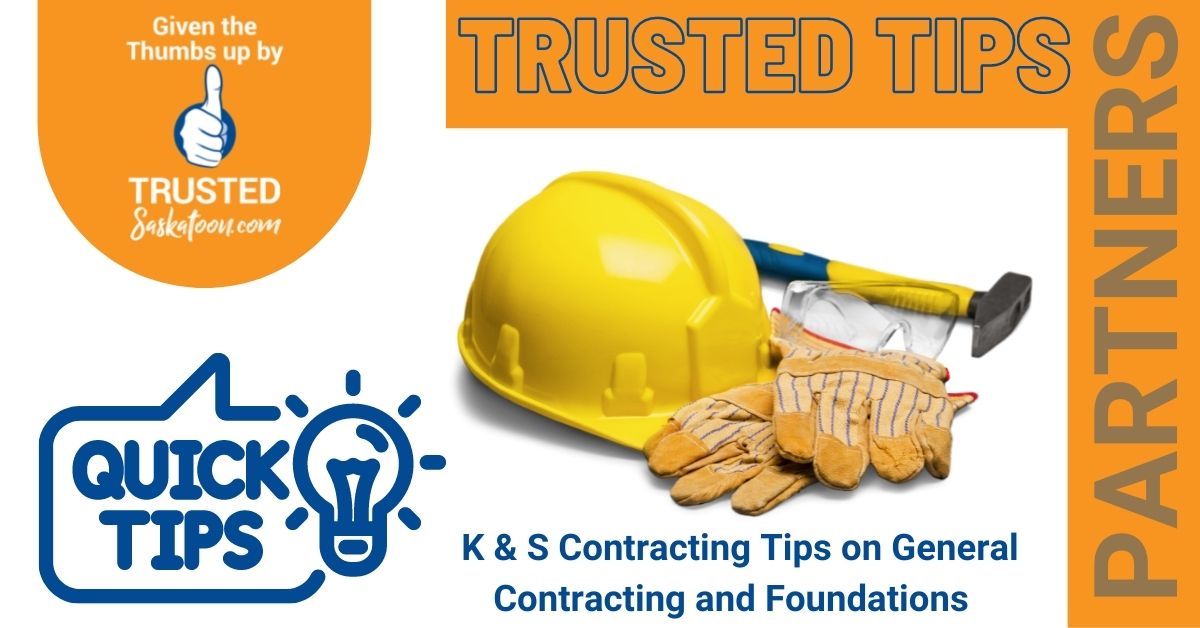
When you see a crack in your concrete slab or wall, generally your first assumption is something has been done wrong–but that’s not always the case. Concrete cracks are very common, some are even inevitable, but let’s review them:
BASEMENT FLOOR CRACKS
Floor cracks in concrete slabs are relatively common and usually not worrisome on a structural level. They should be repaired to prevent common issues like moisture, insects, and damage from seeping through. When floor cracks leak, it is usually caused by hydrostatic pressure or a high water table. Therefore, sealing the crack will redirect those issues elsewhere.
VERTICAL AND DIAGONAL FOUNDATION CRACKS
Usually, a diagonal or vertical crack in the foundation wall is the result of settling in the concrete foundation and is quite common in new construction, especially if your home is built on a hill or your home has rapidly deteriorating soil conditions because of drought or heavy rainfalls. They usually run vertically or diagonally, are often located in the middle section of walls and are less than 1/8 in wide.
Frequently you will find vertical cracks in block foundations. If the crack is located closer to a corner and is wider than 1/8 in, it is probably not due to shrinkage but indicates a more serious foundation issue. It is recommended you
call K & S Contracting to get it inspected as it may be a cause for concern.
HORIZONTAL FOUNDATION CRACKS
Horizontal cracks that run across your foundation and/or walls are some of the most serious types your home can suffer. They indicate a severe issue with your foundation’s integrity that must be looked into.
Most horizontal cracks are caused by excessive water pressure from outside. In addition to other sources of pressure such as soil movement, it has the potential to impact your foundation’s integrity. They tend to expand and ruin the slab itself, possibly even causing it to collapse.
STAIR STEP CRACKS
Stair step cracks are among the most common foundation cracks. These cracks are a clear sign of a problematic foundation. Typically, stair step cracks in a block foundation are a result of bowing walls. These cracks will be found toward the corners of the foundation, and are often found with a horizontal crack. In a block foundation, stair step cracks may also be found on the outside of the home. Stair step cracks always require further investigation in order to keep your home safe and supported.
Questions or concerns, about your concrete foundation cracks, and what they mean, please contact K & S Contracting.
K & S Contracting specializes in foundation repair for homeowners across Saskatchewan, in addition, they also offer general contracting services to Saskatoon and the surrounding area. In their latest Trusted Saskatoon contractor tip, K & S Contracting Trusted Saskatoon General Contractors and foundation specialists, discuss vermiculite insulation.
Vermiculite Insulation - What Is It?
If you have never seen vermiculite insulating an attic, it looks similar to little squares of coloured glass or little grey beads. Vermiculite is a naturally occurring mineral worldwide. When heated rapidly to high temperatures, this crystalline mineral expands into low density, accordion-like, golden brown strands. In fact, its worm-like shape is what gives vermiculite its name. The worms are broken into rectangular chunks about the size of the eraser on the end of a pencil. In addition to being light, vermiculite chunks are also absorbent and fire retardant. It also makes a good insulating material.
Where Was It Used?
Sold under various brand names, such as Zonolite Attic Insulation, the insulation came in big bags. Thousands of homeowners simply opened the bags and poured the vermiculite onto their attic floor and sometimes down exterior walls. It was generally not used in new construction.
When Was It Used?
Worldwide, vermiculite has been used in various industries as long ago as 1920. With the upsurge in homeownership during the baby boom, vermiculite insulation was a popular material in the 1950s and continued with the energy crisis into the late 1970s. In Canada, it was one of the insulating materials allowed under the Canadian Home Insulation Program from about 1976 to the mid-1980s. There have been some government-provided grants offered to homeowners to increase insulation levels, reducing energy consumption. Worthwhile checking in to see what may be available.
What Is The Problem?
The majority of the vermiculite used worldwide was from a mine in Libby, Montana, owned and operated since 1963 by W.R. Grace. The mine was closed in 1990. As well as being rich in vermiculite, this mine had the misfortune of having a deposit of tremolite, a type of asbestos. When the vermiculite was extracted, some tremolite came in with the mix. For Canadian use, the raw product from the Libby mine was shipped to Grace subsidiary F. Hyde processing plants in Montreal, St. Thomas, Ajax and Toronto, and Grant Industries in western Canada. At these plants, it was processed and sold as Zonolite.

What Is The Risk?
Asbestos minerals tend to separate into microscopic particles that become airborne and are easily inhaled. People exposed to asbestos in the workplace have developed several types of life-threatening diseases, including lung cancer. Workers in and around the Libby mine developed serious health problems.
Like any hazards, length and intensity of exposure are major factors in the risk of asbestos-related respiratory illness. To assess the risk of asbestos exposure at a house, a sample of the vermiculite would need to be analyzed by a lab. Since most of the vermiculite used in Canada was taken from the Libby mine, the odds are quite good that there is asbestos in the vermiculite in Canadian attics.
The good news is that we don’t live in our attics. In addition, as long as it is undisturbed, neither the asbestos fibres bound up in the vermiculite chunks nor the dust will be released into the air. According to the National Institute for Occupational Safety and Health in the U.S., “Most people who get asbestos-related diseases have been exposed to high levels of asbestos for a long time.” Lastly, most of the time the air in your house flows from the house into the attic, rather than into the house from the attic.
The bottom line is, like most household products that may contain asbestos, and there are many, doing nothing is often the best approach. Naturally, the risk of exposure increases with the amount of time spent in the attic.
Our Recommendations
If the attic or walls of a house contain vermiculite insulation, leave it alone. Avoid disturbing the material. Do not sweep it or vacuum it up. Do not store belongings in the attic.
If work is planned that involves these areas, for example installing pot-lights in a room below the attic, send a sample of the vermiculite to a private lab. Send several samples, and use a lab specializing in asbestos analysis. If it is found to contain asbestos, or if you just assume it does, precautions should be taken. The safest approach would be to have the insulation in the affected areas removed by a qualified environmental contractor.
For smaller jobs, it may be sufficient to isolate work areas with temporary barriers or enclosures to avoid spreading fibres, use disposable protective clothing, and use proper respiratory protection. An important note – disposable respirators or dust masks are not appropriate for asbestos. Again, it is best to consult a qualified contractor.
Wood FX Contracting is a Saskatoon family owned and operated with over 18 years experience. Their carpenters and renovation team consist of hardworking individuals ready to tackle your interior home renovations - big or small! They are on-site daily ensuring client satisfaction. In this article, they explain what the Janka Hardness Scale is. Wood FX are Trusted Saskatoon Carpenter and Renovation Pros!
The Janka Hardness Scale
Hardwood flooring is one of the best decisions you can make when it comes to interior home design, as it is a product that never goes out of style. It’s easy to assume that all hardwood flooring is the same when it comes to durability, but this is actually quite far from the truth. Hardwood’s actual hardness is measured by something called the Janka hardness scale. Let’s take a look at what the Janka scale is and how it works.
What is the Janka Hardness Scale?

The Janka hardness scale is a way of measuring the hardness of a given piece of hardwood. It was invented in the year 1906 by an Austrian wood researcher named Gabriel Janka, and it is an adaptation of the Brinell hardness test for metals. In order to better understand the Janka scale, you first need to know how the Brinell test works. The Brinell hardness test is used to test metal materials that are too coarse or rough to be tested by other means. The test involves a steel ball with a 10mm diameter being pressed into the material’s surface under 3,000 kgs of pressure. The resulting indentation is then examined to determine the hardness of the material.
How Does the Janka Hardness Scale Work?

The Janka hardness scale works in a very similar way to the Brinell test. It measures the pounds of force (lbf) it takes to drive an 11.28 mm diameter steel ball halfway into the surface of a slab of hardwood. A test done on the surface of a board, perpendicular to the grain is called a test of “side hardness”, while the same test being performed on the cut surface of a stump is called a test of “end hardness”. Every hardwood board will not yield the same test result, seeing as the hardness of wood varies with the direction of the wood grain, and will be different from one board to another. While durability issues come up when we look at different types of wood grains, there is usually not much deviation when it comes to differences in separate types of wood material, as estimates usually find the difference to be about plus or minus 10%.
Why is a Janka Hardness Rating Important?

Hardwood flooring is a big investment and will typically cost you a pretty penny, so you’ll want to make sure you are getting top quality wood that is not going to deteriorate or wear down after a few short years. While wood with a low Janka rating can still serve you just fine, it is only going to do so if you live a quieter lifestyle that does not involve your home seeing heavy foot traffic. If you have children and/or pets, try to find hardwood with a higher Janka score. A Janka hardness rating is going to give you a great indication of what kind of wear and tear your hardwood is going to be able to handle, helping you make a smarter decision when it comes to making a purchase.
.jpg)
K & S Contracting specializes in foundation repair for homeowners across Saskatchewan, but they also offer general contracting services to Saskatoon and surrounding area.
In this Trusted Saskatoon Tip, K & S Contracting discusses preparing your basement for renovation.
Preparing Your Basement for Renovation
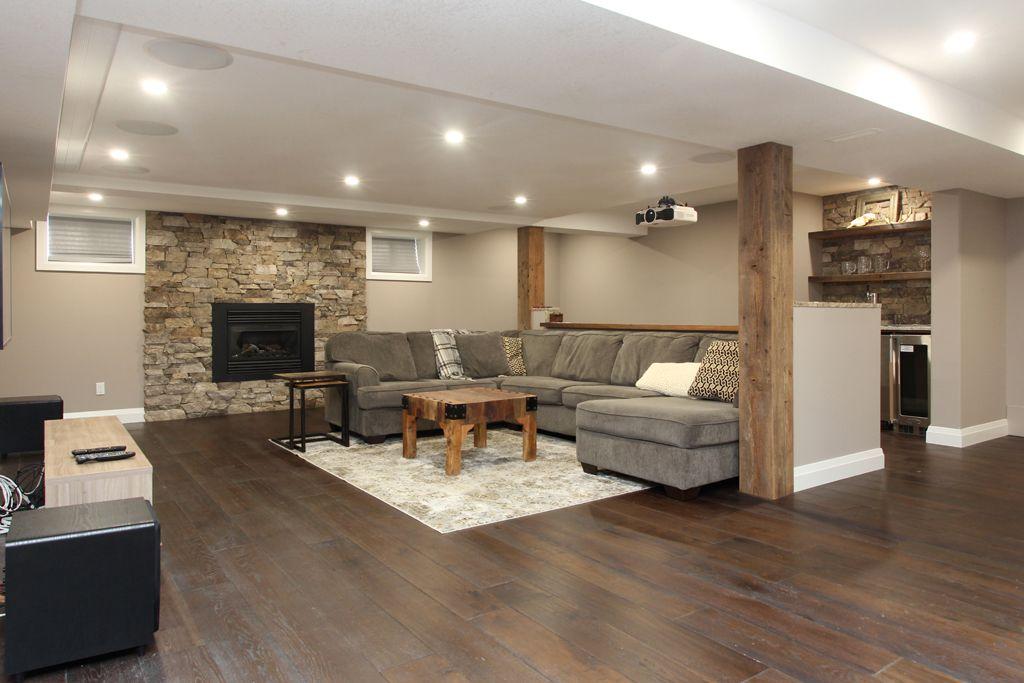
A finished basement is a great space to entertain, relax, or pursue hobbies. Turning a cold, empty, concrete basement into an enjoyable living space takes work and planning. There are a lot of design and functionality options which are up to personal choice, but there are some basic considerations to keep in mind for anyone planning a basement renovation. Before you start, take these tips into consideration for a smooth and successful Renovation.
Start with the Layout
Plan how the room(s) in the basement will be laid out. Any bedrooms must have windows for safety. Put the main socializing area in a spot with good natural light to draw people in. If you are planning on having a TV viewing room it can be in the darker area away from the windows to reduce glare.
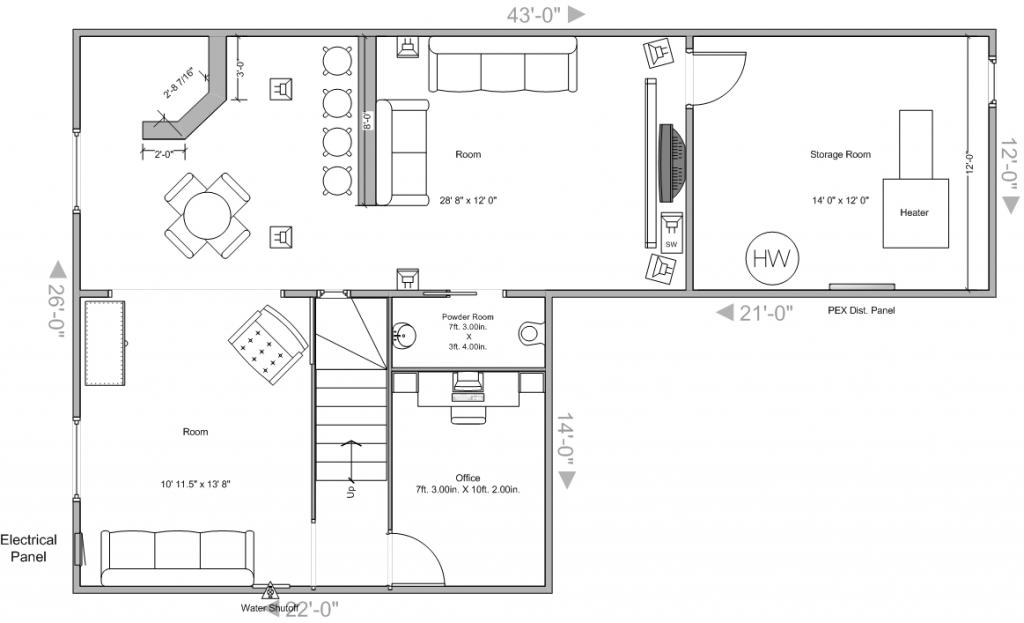
What to Fix Before You Start Renovations
Check for moisture by taping some squares of plastic over the walls and floors. If moisture forms underneath, your basement foundation is likely not sealed. If moisture forms on top, the basement needs dehumidifying.
Small leaks in the foundation can be dealt with yourself using some concrete-patching compound. Landscaping considerations such as sloping away from the foundation and installing gutters that send the water far from the foundation will also help. Any cracks in the foundation wider than a pencil should be checked by a professional structural engineer.
Insulate any exposed water pipes with foam insulation sleeves, and insulate any exposed wiring with high-temperature grade red silicone. If you feel uncomfortable working around electrical wires, have a professional take over this part. Have a professional check the integrity of floor joists, and inspect any fuel burning equipment and the ventilation system to ensure you won’t have carbon monoxide buildup.
Now You are Ready to Start the Renovations
Now that the basement is ready to go, you can start the actual work! If you would rather not DIY a major project like a basement renovation, the Trusted Contractors at K & S Contracting are ready to help!
Their services include:
K & S Contracting specialize in foundation repair for homeowners across Saskatchewan, but they also offer general contracting services to Saskatoon and surrounding area including:
In this Trusted Tip, A“It’s time to let go of our
ideas about dated faux wooden paneling, and check out these new ideas with
laminate on your walls!”
What can laminate do for the walls in your home? I am so glad you asked!
- Laminate can add a great rustic feature wall in your bedroom.

- It can be used instead of flashy wall paper.
- It can provide your bedroom with a traditional headboard.

- It can add warmth or a unique artistic feature in your home.

Laminate is a great option to create any of these looks.
There are so many affordable options to choose from and can be quite quick to install.
READ MORE CLIENT REVIEWS HERE ON THEIR WEBSITE K & S Contracting are Saskatoon’s Trusted Contractor for ICF Foundations..."They will get you back on solid ground!"
K & S Contracting are Trusted Saskatoon General Contractors and foundation specialists